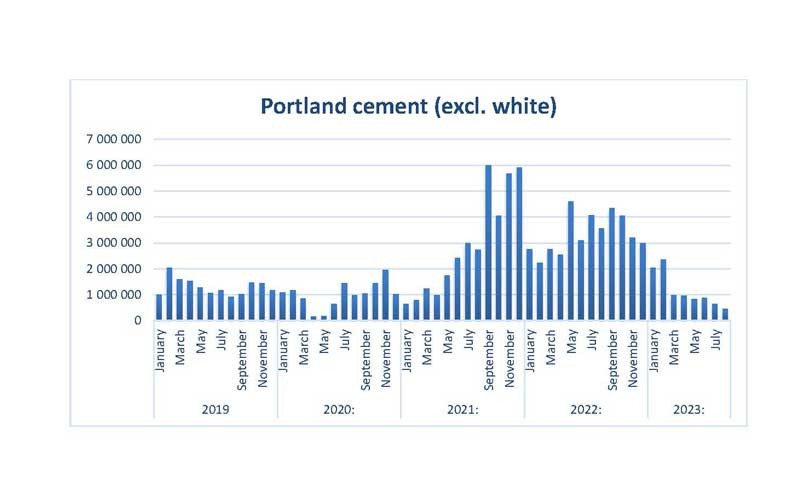
THERE is no doubt the construction industry in Zimbabwe is growing. Densification through cluster development is now the new anthem in town.
According to research by Injecta Analytics, there are more cluster housing units in Newlands than residential stands. Around 39 cluster developments have added 442 new housing units in Newlands, which originally had 425 stands.
The target in the National Development Strategy 1 is to build 225 000 houses by the end of 2025. On the other hand, other infrastructure developments in the form of dams, border posts and roads amongst others are also not only ongoing but at a massive scale. Essentially, we have been witnessing a construction boom in the past half a decade or so.
Central amongst all these construction activities is a product called cement, whether road construction or otherwise, it is needed. According to Pretoria Portland Cement (PPC), a regional cement producer, Zimbabwe’s cement consumption per capita in 2022 was 89 kilogrammes.
This puts our consumption ahead of peers like Rwanda and the Democratic Republic of Congo (DRC). However, South Africa and Botswana’s consumption is ahead of ours.
Currently, Zimbabwe has five different cement producers with PPC having the lion’s share, controlling 60% of the total market share. Ekhaya, formerly Lafarge Cement, produces approximately 16% of the market share. However, since the company restructuring its share might have changed.
Zimbabwe has the capacity to produce 2,6 million tonnes of cement annually with PPC contributing over 60% of that. Despite national cement demand being between 1,3 million to 1,6 million tonnes, we find ourselves in a situation where there is a shortage, which is usually filled by imports.
Also, to protect local industries, in April 2021, the Ministry of Industry and Commerce issued Statutory Instrument (SI) 89 of 2021.
- Lafarge account garnished over debt
- Cambria hits brick wall on OM shares
- Sino-Zim disposes of Allied Insurance shares
- Fossil Mines concludes Lafarge takeover
Keep Reading
Essentially, this SI requested that a licence be required before cement is imported into the country. Interesting enough, based on the trade numbers below, the cement imports did not immediately drop, instead they increased and only started to decrease this year.
All these numbers might fail to make sense until you look at the cost of manufacturing cement and the selling price. According to PPC, the highest EBITDA margins in their segment analysis were reported in South Africa and Botswana at 51% whilst Zimbabwe was 26%.
Using EBITDA margins as a rough estimate of operating costs and cost to produce, we can conclude that it is cheaper to produce in South Africa and Botswana than in Zimbabwe.
To substantiate this claim, one would further look at the prices of cement in the region. Before this new wave of price increase, a PPC 42,5 bag of cement was going for US$6,50 in South Africa and US$11,50 locally.
An equivalent of that, although different brands fetch US$6,50 in Zambia, whilst in Kenya and Nigeria it is US$5-6 and US$8-9, respectively, according to a desktop research I conducted online. Now the word around the market is that cement supply is low and the demand is now pushing prices higher. Prices of that similar bag of cement are now getting as high as US$17 and securing one is still not easy.
The increase in demand has become seasonal over the years and the fourth quarter coincides with a period of diaspora market coming back home and increasing activity in the construction space.
However, imports have been able to meet the increase in demand and clearly this year, the imports have dwindled contributing to the crisis that the market is currently experiencing.
Analyst’s comment
Although it might be temporary, I opine that the spike in cement prices negatively affects the pace at which construction projects are carried out in the country.
Notwithstanding the need to protect our local manufacturers, I think it is high time those local manufacturers become competitive in terms of both quality and pricing.
With the coming of the African Continental Free Trade Area, protecting industries by imposing quotas and tariffs might not work, hence the need to be competitive.
In the short run to ease the pressure, I opine that imports might be necessary whilst the long-term plan would be to increase the local production to reach its full capacity.
If Zimbabwe were to produce competitively at full capacity, it perhaps would even export some of the cement to its peers. As Khaya Cement concludes its corporate restructuring exercise and increases its capacity, there could also be another increase in the production of cement.
The construction exercises in the country are nowhere near completion; the housing deficit is estimated to be between 1,5 million – 2 million units while road rehabilitation exercises amongst others will continue for the foreseeable future. This calls for a long-term solution to the crisis.
- Hozheri is an investment analyst with an interest in sharing opinions on capital markets performance, the economy and international trade, among other areas. He holds a B. Com in Finance and is progressing well with the CFA programme. — 0784 707 653 and Rufaro Hozheri is his username for all social media platforms.