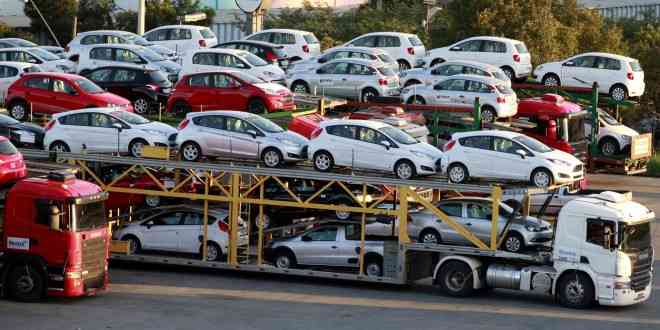
THERE are only a few nations, which can build cars from scratch. Unfortunately, Zimbabwe is not one of them.
Even the most advanced automotive industry in Sub-Saharan Africa (South Africa) sources key powertrain (engine), drivetrain (transmission, gearbox, etc) and telematics (GPS systems, on-board vehicle diagnostics, wireless device connectivity, etc) technologies from top automotive countries, which produce more than 1,5 million vehicles per year.
In contemporary vehicles, powertrain, drivetrain and telematics make up about 50% of the vehicle's value. Generally, South African manufactured vehicles contain 40% local content, which mostly comprises the steel, seats, batteries, glass, tires, etc.
The 40% local content effectively means that of the 520 000 vehicles, which the country manufactures each year, it can effectively lay claim to only 208 000 (40% x 520 000).
Experts there also have great concern that as international manufacturing technologies advance, their industry risks losing viability. With such a background characterising advanced regional manufacturers, Zimbabwe's own automotive industry is also not guaranteed continuity.
Zimbabwe has four key vehicle manufacturers (assemblers), who include Quest Motors Corporation and Willowvale Motor Industries, which specialise in passenger vehicles.
There is also Deven Engineering and AVM Africa, which focus on the building and refurbishment of buses. The country has ayearly vehicle demand of around50 000 used carsand 500-800 buses.
Brand new vehicle imports are still a tiny fraction, at around 4 000 per year. The automotive industry in the country has the capacity and potential to impact local employment.
- Zim headed for a political dead heat in 2023
- Record breaker Mpofu revisits difficult upbringing
- Tendo Electronics eyes Africa after TelOne deal
- Record breaker Mpofu revisits difficult upbringing
Keep Reading
For instance, Quest Motors can employ up to 4 500 workers when operating at full capacity (producing 10 000 passenger cars per year). AVM Africa also used to employ up to 2 500 workers at its peak, whilst it was a major exporter in the Sadc region.
If the other two assemblers are included, then the total employment that could be realised from the four assemblers may range between 9000-12 000. If the manufacturers were to also branch into agricultural equipment, such as tractors, there will be even more benefits for them, local farmers and the overall economy.
Challenges in the local industry
Several challenges characterise the local automotive sector. Firstly, the massive used car imports are a major threat, which can drive some of the assemblers into liquidation (to close down operations).
A major problem with letting these manufacturers exit the industry is that, once expertise is lost, it may be difficult and sometimes impossible to recover.
Secondly, the country imports the core technology used in locally assembled vehicles and in some cases, the foreign content may even be so much, to the level where there is extremely minimal local content in the final product.
When assemblers import semi-knocked-down vehicle units for instance, only negligible local content can be constituted in the final product. However, Quest Motors and AVM, insist that the level of local content in their final products is significant.
Thirdly, the challenge of power outages is limiting progress and increasing costs for some of the assemblers. Additionally, for small manufacturers of components (batteries, auto glass, springs) costs of production and product prices can be exceptionally high, due to lack of economies of scale, owing to the small production runs.
Moreover, the fact that Zimbabwe does not have a national vehicle brand shows that the country does not have much to show in terms of technological prowess.
It is disheartening that with all the students and professionals in science and technology, the country has not managed to design its own vehicle engine, even one which operates on mechanisms that were developed in the early twentieth-century (the 1900s).
That should be a cause for concern because the expertise used in the automotive industry can also be applied in other manufacturing sectors. The skills can be used to guide the development and maintenance of various machinery used in Zimbabwean industries.
Once the country challenges itself to build automotive machinery, there will be stronger hope for economic advancement. As long as Zimbabwe lags in these areas, it will continue exporting unprocessed minerals (iron ore, chrome, lithium, etc) only to import the more expensive manufactured goods.
China, for instance started building its own vehicle engines in the 1930s, whilst it was a poor country, with some of the engines running on charcoal, as an innovation to circumvent petrol and diesel shortages at the time.
Solutions
As a starting point, the government may need to support local bus manufacturers, instead of encouraging bus imports. In that regard, government’s invitation to tender for the supply of 500 buses, which closed on January 26, may need to be re-looked. Instead of choosing imports, Treasury has a crucial chance to support local bus assemblers, with this pending order.
Such orders can go a long way in improving local levels of employment. The only precondition, which may need to be fulfilled is that, the domestically produced buses should have considerable local content.
When interviewed by the media in September last year, Carl Fernandez, the general manager of Quest Motors, outlined that locally made buses are cheaper than imported ones since they cost about US$20 000 less. Moreover, local manufacturers can make designs, which are compatible with domestic conditions. It can be easier for the country to have custom made buses with high ground-clearance, which is suitable for the domestic landscape and some of the gulleyed roads.
It will also be crucial for the country to have a government branch, which focuses on machinery development, including engines and vehicle technologies.
Coordinating and supporting developments in this area at the highest level will be crucial in order to develop industrial activities, which are independent of reliance on tools and componentry from the northern economies.
It will serve the country with good precedence if locals can have the opportunity to design and actually build vehicles. Since mass production requires heavy investments, the country should at least be capable of manufacturing handmade vehicles, which are typically produced in small quantities although most of such, are also extremely expensive in the car market.
There should be an end in sight to the perpetual extraction of iron ore, chrome, lithium and other raw materials destined to the northern economies, only for Zimbabwe to have contact with its resources again, as more-expensive manufactured imports.
Government should also target to draw globalvehicle manufacturers to establish production plants in the country. The massive car output from the industries will then be used to supply foreign markets.
In this regard, it will be critical to state that, the most prominent car manufacturing countries on the continent (Morocco and South Africa) depend onexport markets for much of their vehicle sales.
Zimbabwe needs to engage prominent international brands, such as BAIC, GWM, BYD, Toyota, Nissan, Peugeot and Mercedes Benz, among others.
The country has multiple benefits, which should give it a good chance to be seriously considered by the international brands. Firstly, there are abundant mineral resources (iron ore, nickel, chrome, lithium, etc), which can be used in the production chain.
Secondly, the country has abundant water, which is a key requirement of major vehicle production plants.
Thirdly, Zimbabwe has close geographical access to various ports (Walvis Bay, Maputo, Beira, Durban, Port Elizabeth, Dar Es Salaam), which make it possible for it to expedite exports to the American, European or Asianmarkets.
More importantly, Zimbabwe enjoys free trade agreements with some essential vehicle consumer markets, such as Europe. If the country is to utilise its preferential trade agreements to the highest level, it will need to draw such major manufacturers.
Renault managed to establish a plant in Morocco, in 2012, based on some of the outlined advantages. Peugeot also followed and built its own plant in 2019.
To date, the Renault and Peugeot plants in Morocco now produce 400 000 and 200 000 cars, each year, respectively. The automotive industry now contributes up to 19% of the nation's gross domestic product (GDP). Zimbabwe may need to try its chances with such manufacturers as they offer the possibility of bringing sudden shifts to employment levels and economic growth. The presence of global manufacturers in Zimbabwe, will ultimately justify stringent rules and duties, on second-hand car imports, as they will be able to satisfy, whichever level of domestic demand.
Infrastructural requirements
Automotive industries will need dedicated industrial parks, which enable them to have uninterrupted access to electricity, water and telecommunications connectivity.
The railway infrastructure will need to be in excellent condition in order to ensure reduced cost of logistics. Therefore, if the government desires to engage such manufacturers, it should be ready to assist with the development of these infrastructure.
Additional electricity generation capacity will be needed as the current 1600 MW (average effective supply) will be much below the demand of such industries. Tax incentives may also be offered in order to make the country a more attractive destination.
Lessons from China
After China had developed its own engines in the 1930s, it set itself on a path to design and produce professionally made and internationally comparable vehicles.
To achieve this, in the 1950s, it sought assistance from the Soviet Union (a grouping of states led by Russia) and received the requisite engine and design technologies to guide the process. From that time (the 1950s), the country had low production numbers, until it introduced its "Law on Joint Venture Using Chinese and Foreign Investment", in July, 1979.
The legislation required that all foreign vehicle manufacturers wishing to produce their products in China be in a joint venture with at least one Chinese vehicle manufacturer.
Through this initiative, Chinese brands managed to access the latest car-making technologies (especially from the West) until they rose to prominence, making China the largest manufacturer and exporter of vehicles in the world.
Government support continued in China, as subsidies and other assistance continues to be offered to manufacturers of New Energy Vehicles (NEVs), in particular.
Estimates of government support in this sector, from 2009-2022, range between US$28-US$57 billion. Until 2022, Chinese citizens used to enjoy government-funded discounts of up to US$1 800 (¥12 600) for each New Energy Vehicle purchase.
The resultant increase of NEV sales has enabled local producers to gain specialised knowledge and techniques in this segment.Consequently, Chinese manufacturers have become so skilled and successful with NEVs such that, the most prominent global brands (Toyota, Mercedes Benz, Renault, Nissan, etc) are now flocking to also develop joint ventures with them, so that they get access to their technologies in this field.
A major lesson for Zimbabwe here, would be that alliances with bilateral partners (China, Russia, etc) should graduate from begging aid and manufactured products to well-established technological exchanges, which can capacitate the country's manufacturing sector to develop its own inventions.
If China had limited its 1950s relationship with Russia to that of humanitarian aid and debt, it would not have developed the most successful automotive industry in the world, as it has managed to do today.
- Tutani is a political economy analyst. — tutanikevin@gmail.com