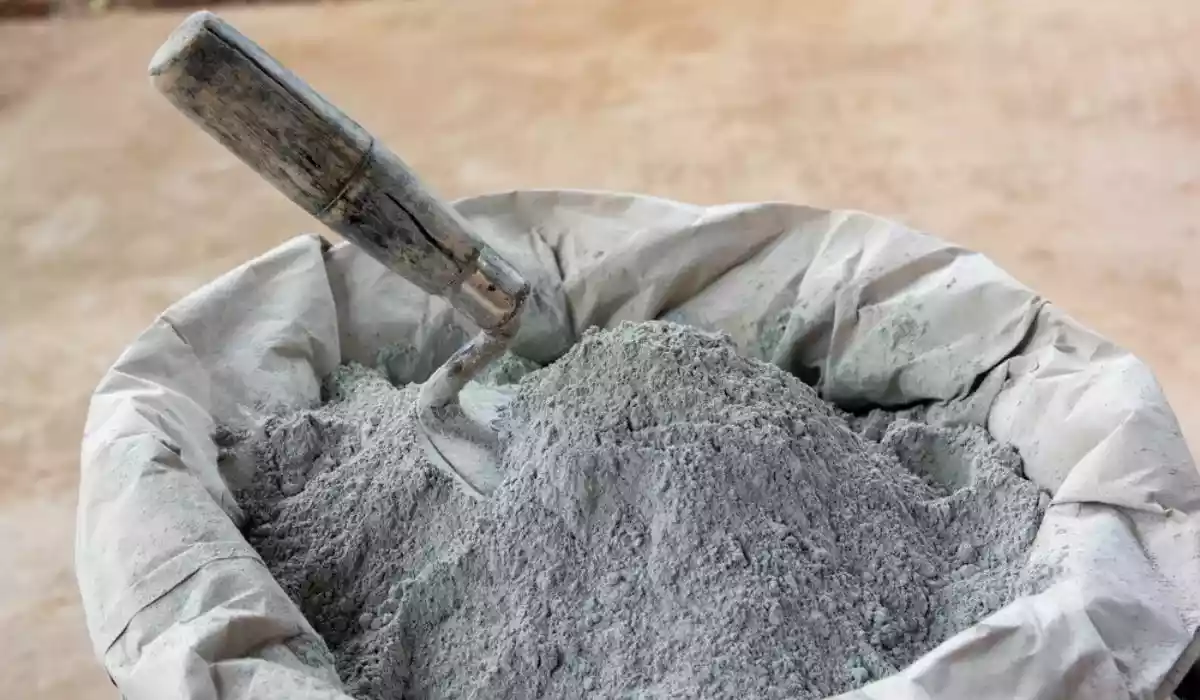
THE government reportedly gave in to pressure from contractors, who stormed the Ministry of Transport offices last week, demanding a solution to the skyrocketing cement prices that threatened the progress of most infrastructure projects in the country, the Zimbabwe Independent can reveal.
Government liberalised cement imports this week on Tuesday to mitigate against shortages. This was after prices doubled in the past two months, a development which riled activists advocating for greater use of locally manufactured products.
Industry sources also claimed the shortages were being driven by a cartel seeking to benefit from rising demand of the product because of ongoing infrastructure projects.
The dire shortage of cement and the spike in prices due to increased demand in Zimbabwe reportedly stalled a lot of infrastructure projects, including government-funded ones.
A 50kg bag of cement, which previously retailed between US$9 to US$13, is currently selling between US$16 and US$20, leading to a spike in the cost for ongoing infrastructure projects.
In 2021, government restricted cement imports in response to local manufacturers, who feared a flood of cheaper cement could lead to business collapse.
But local manufacturers — PPC, Khaya and Sino Zimbabwe Cement — who have a combined capacity of 2,6 million tonnes annually, are unable to meet demand due to a variety of reasons, including plant breakdowns, maintenance and higher production costs.
PPC has capacity to produce 1,6 million tonnes annually, while Khaya is at 500 000 tonnes and Sino Zim is at 200 000 tonnes.
- Accidents: MP appeals to Transport ministry
- Govt suspends licences of Rimbi and Zebra Kiss buses after fatal accident
- Act now to curb road carnage
- Health talk: Lack of political will pushing health sector into abyss
Keep Reading
The Independent is informed that a team of contractors recently stormed the Transport ministry offices in Harare demanding a restructuring of contracts to consider the spike in prices triggered by the unavailability of cement on the local market.
The contractors were threatening to abandon projects until the government had addressed their grievances.
Most projects under the Emergency Road Rehabilitation Programme (ERRP 2) in Bulawayo have stalled over cement shortages. Some of the cement purchased about a month ago has not been delivered yet.
“The situation had become tense in government corridors as contractors kept knocking on doors asking for a solution. Some were demanding a restructuring of contracts because the recent spike in cement prices had gone beyond the expected margins,” a source close to the developments said.
Soaring cement costs and concrete shortages have proven to be a threat to infrastructure development, while low supplies affect the booming residential construction industry.
Efforts to get a comment from Khaya Cement and PPC, the country’s biggest cement producers, were futile.
Transport minister Felix Mhona did not respond to questions sent to him.
However, Buy Zimbabwe chairperson Munyaradzi Hwengwere said they were expecting to meet with cement manufacturers to get details on what is happening in the industry.
“Our management team is seeking to engage the cement manufacturers so that we have a better view of the issue. As Buy Zimbabwe, our view is that it must be local-based because it is the locals that create jobs,” Hwengwere said.
“But we have also been clear as Buy Zimbabwe that as much as local is critical, it must be local that thrives to be competitive. We are trying to gather full facts so that we have an understanding, but we have a basic view that locals first, but locals must not mean mediocre. They must also strive for competitiveness.”